How we clean the exhaust
Content
- Solvang's total emission control system
- Onboard carbon capture and storage (OCCS)
- Solvang's EGC and low-pressure EGR setup
- Washwater management and samples (data sheet)
- References and articles
- WESP - the wet electrostatic filter
- GHG reduction for different shipping fuels
- Life below water - our footprint
Solvang's total emission control system
Solvang runs a low-pressure exhaust gas recirculation system for NOx-TIR III control on main engines, combined with an exhaust gas cleaner (EGC/scrubber), in order to convert the sulphur in the fuel into sea salt. We use a hybrid exhaust gas cleaning system with electrostatic particle filters (WESP) for SOx and particle control onboard five vessels, and scheduled for installation on seven VLGC newbuildings.
A pioneer of OCCS - onboard carbon capture
In 2023, Solvang received a grant of MNOK 80 from the Norwegian Climate and Energy Fund, in order to apply OCCS in operation. At the turn of the year, OCCS was being installed onboard the LPG carrier Clipper Eris. The system captures CO2 from the 7 MW main engine, before it passes through the exhaust outlets. Inside the smokestack, carbon gas is being separated, then refrigerated into liquefaction and transferred to deck storage. The installation is set to capture 70-80 percent of carbon dioxide from the main engine and auxiliary engines’ outlet, dramatically improving the ship’s environmental performance.
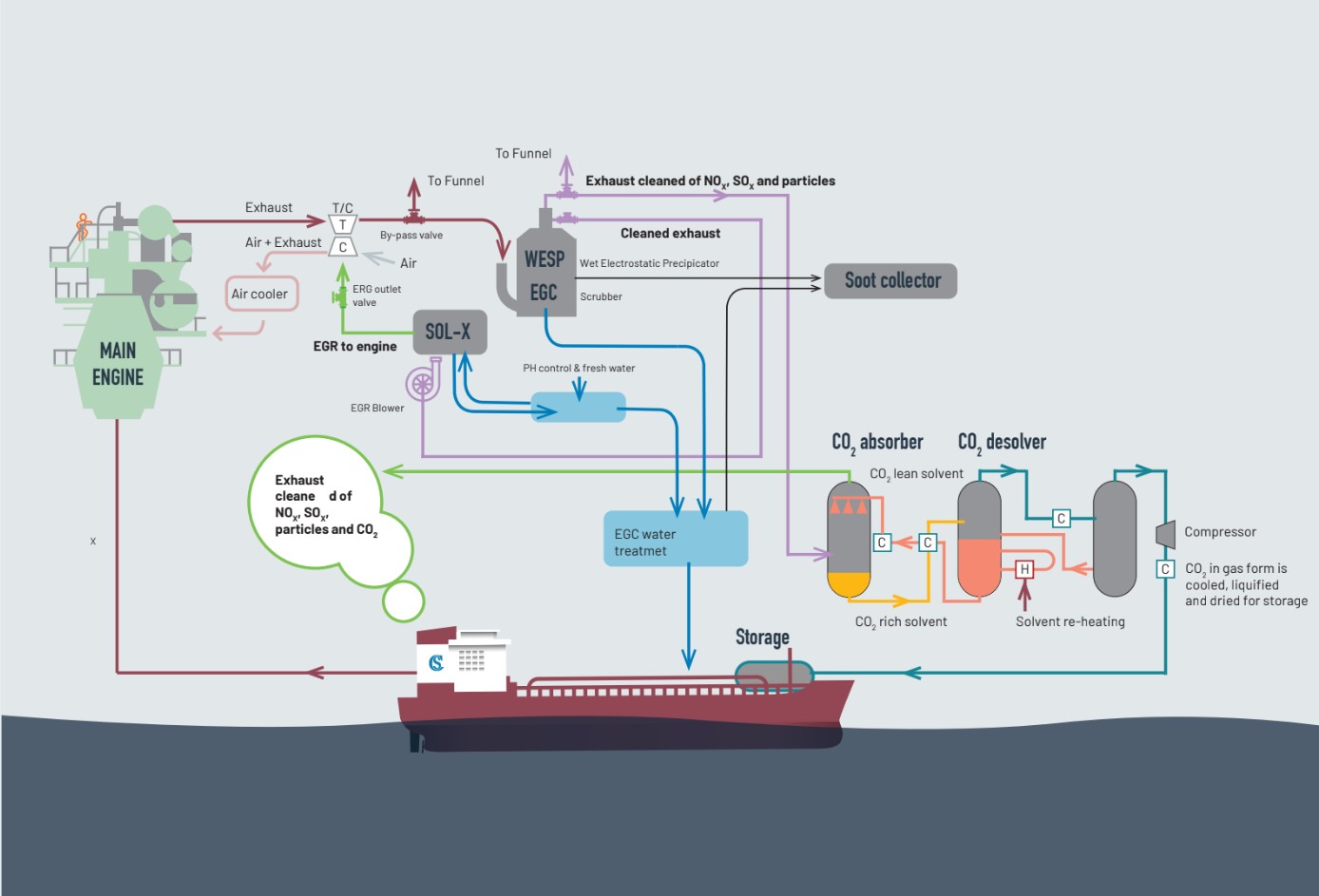
Solvang's EGC (scrubber) and low-pressure EGR setup
Solvang commenced its low-pressure EGR project with former gas tanker Clipper Harald in 2015, which showed continous HFO operation below NOx TIR III levels, without the use of urea. In 2019, the setup was extended to four 21,000 cbm ethylene carriers and one 80,000 cbm gas tanker.
The concept has been further developed to cover seven VLGC newbuildings scheduled for delivery from 2026.
The figure below shows an historical fuel burning reduction of 60 percent, NOx and particles reduction of 90 percent, and SOx reduction of 99.8 percent, respectively.
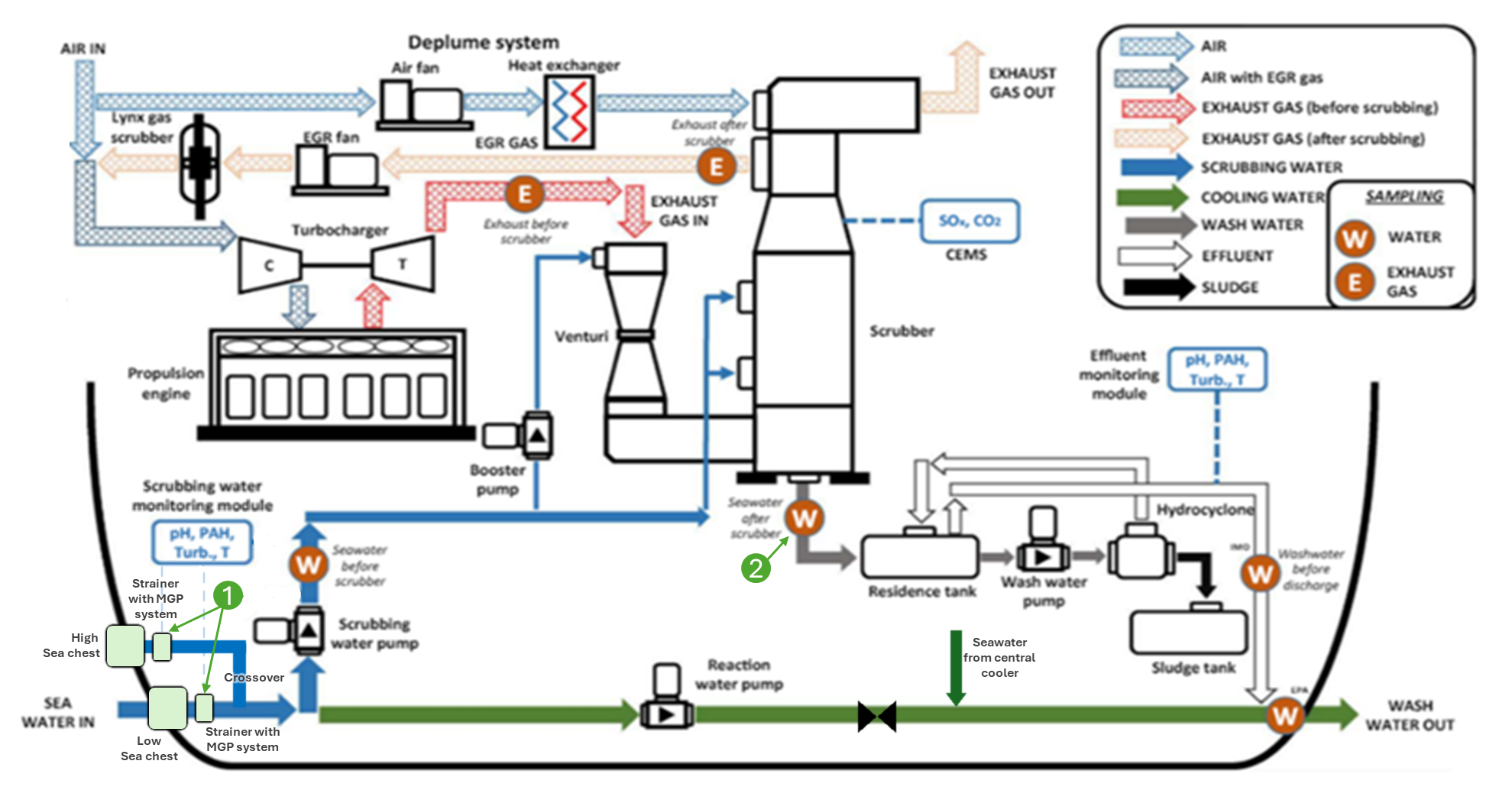
Scrubber pro's
- CO2: Reduced "well-to-wake”
- SOx: Reduced to LNG level
- High-value energy from low-cost residual oil
- Engines already fit for HFO
- Makes cheap fuel pay for NOx cleaning with LP-EGR
- Catches toxic particles in addition to MGO particles
- Prepares for ECO-EGR, TIR II NOx operation with EGR
Scrubber con's
- High investment costs
- Nickel and vanadium accumulation in enclosed harbours
Converting sulfur to sea salt
Solvang utilises calsium carbonate in a seawater scrubber to convert sulphur oxides into sea salt. The sea water flue-gas desulfurisation process (SWFGD) exceeds 98 percent in efficiency, and it yields no by-products. The flipside is a 2-3 percent rise in fuel (HFO) consumption, increasing CO2 emissions correspondingly. The alternative, to crack HFO in an onshore refinery, would increase CO2 emissions by 10-15 percent.
Alstom Sea Water Flue-Gas Desulfurisation process
Sea water salt content
The current natural concentration of calcium sulfate in seawater is 2.7 g/l. If all vessels in the world use fuel oil with scrubber for another 150 years, the concentration of calcium sulfate will rise to approximately 2.701 g/l.This means a seawater scrubber can be regarded as a reactor converting sulfur into sea salt.
Washwater management and sampling
Solvang closely monitors the level of risk posed to humans and nature by our operations. The washwater from exhaust cleaning is analyzed according to PEC/PNEC and Norwegian criteria for metals, PAH components, hydrocarbons, nitrate/nitrite, turbidity and PH, in total 41 components plus PH and turbidity for each sample.
Solvang samples inlet sea water and outlet washwater from the EGC. The method follows IMO guidelines for the vessels' IAPP certificates, and the results show similar figures for the predicted effect (PEC) and no-effect concentration (PNEC). Which indicated that washwater discharges do not affect the surrounding water at this distance or likely anywhere beyond. See Marintek report MT2016 F-152 ("Clipper Harald operation with scrubber").
Solvang submits EGC water samples to maritime authorities for IMO
Download data sheet for verified samples and analyses from 13 vessels, data series 2020-2024
- PPR 12-7-2 - Substances contained in discharge water from exhaust gas cleaning systems (Norway)
- PPR 12-7-1 - Data to be used for the calculation of representative emission factors of discharge water... (Norway)
- PPR 12-INF.11 - Quality Assurance (QA) of the data presented in document PPR 1271 (Norway)
There has been a discussion about the negative impact from open loop EGCS in port and/or special areas. It seems to be large variations in methodology and results regarding water samples from EGC. IMO has therefore asked for validated data to ensure high quality risk assessment regarding possible impacts from the EGCS. An EGC uses the alkalinity in seawater to convert the sulfur in the fuel to sea salt. Basically, EGC is a reactor which converts sulfur into sea salt.
Inflated sample output
Following IMO’s request for data, Solvang has compiled five years of sampling results from 13 vessels. In general, the results show that the EGC contamination is between a 5,000th and 10,000th fraction of the contamination suggested by another dataset recently being submitted to the IMO.
In general, these “tricky” measurements require experience and good procedures to get validated results. The detection limit is in the scale microgram per liter. To understand the scale, with 1 microgramme per liter we need 1 million liters to get one gramme of an element. The emission factor established, is on a scale, 1 million less than standard emission factor to air from ships engine.
In the IMO documents, Solvang has discussed the element measured in the water together with a detailed description of the complete water system, from the sea chest to overboard. The dataset and methodology have been validated by Sintef.
News release: Solvang refutes inflated washwater sampling figures
Nickel, vanadium and copper
The water samples have been compared to Norwegian water quality standard published by Miljødirektoratet.
All metal elements are natural in ambient seawater. Solvang cannot see any particular concern to the use of open-loop EGC at sea and in open ports. The only thing to be aware of is the possible accumulation of nickel and vanadium in closed ports. For copper, a smart control of marine growth system would very easily bring the values within acceptable limits. For a shorter period and in closed ports, MGP could also be switched off.
As part of the unburnt fuel (THC) in exhaust, PAH is being condensed in the scrubber and contained in sea water instead of being released to the atmosphere. Well-maintained diesel engines running on HFO or MGO emit 0.1-0.2 g/kWh. Shipping is estimated to contribute 0.5 percent of the total PAH emissions in Norway (newest data from 2015). Whether PAH emissions with the use of HFO is higher or lower than MGO and 0.5 % HFO we don’t know. In any case, the values are negligible.
Solvang's washwater analyses show less than 10 percent of the maximum ∆PAH levels. PAH carceniogenics are close to or below detection levels.
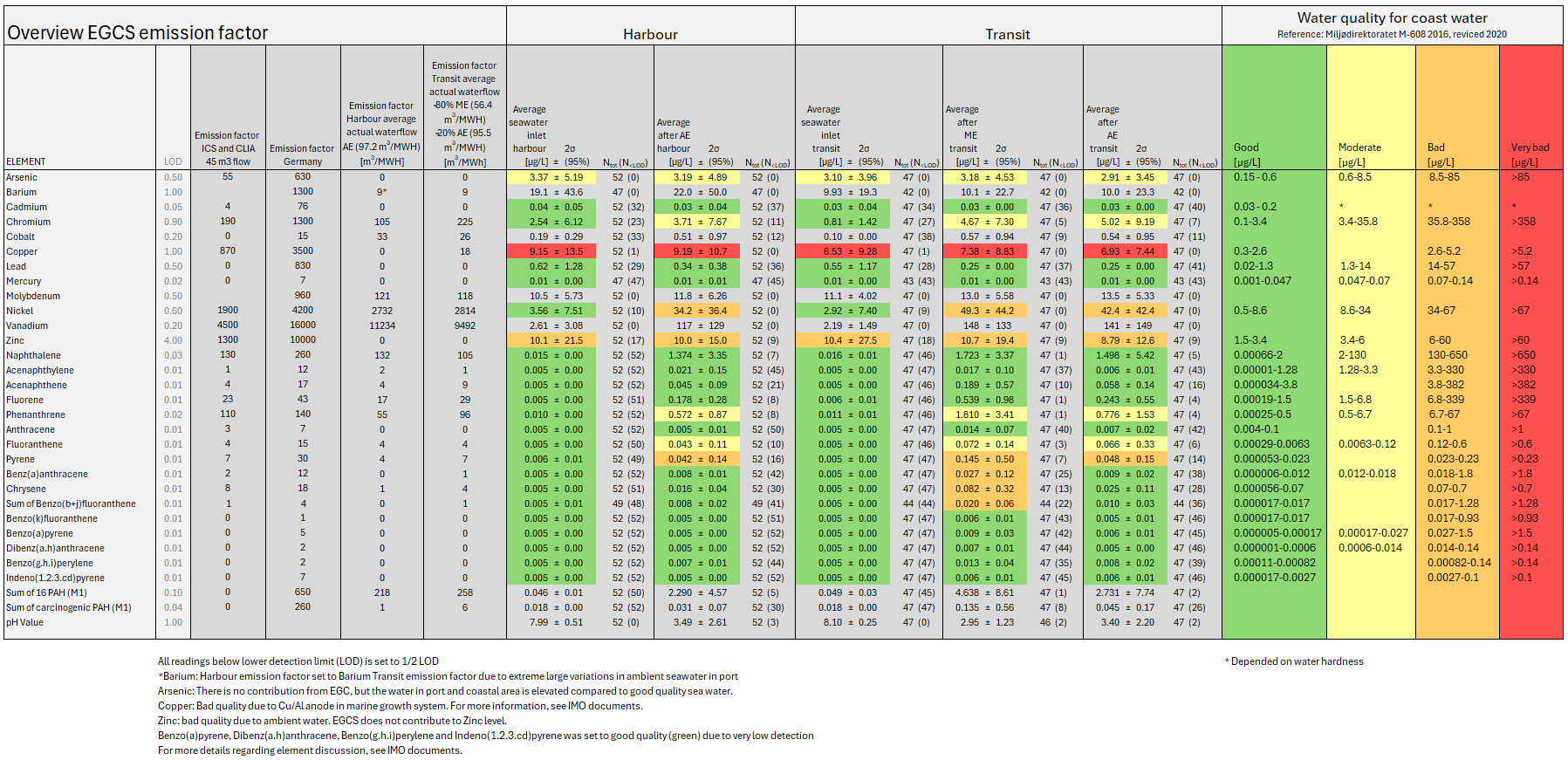
Read more
Marine Scrubbers vs. Low Sulphur Fuels: A Comprehensive Well-to-Wake Life Cycle Assessment
Exhaust gas scrubber washwater effluent | US Environmental Protection Agency
Washwater criteria for seawater exhaust gas SOx scrubbers (Marintek report MEPC 56/INF.5)
Polysykliske aromatiske hydrokarboner (PAH) | Miljøstatus (NO-2018)
Automotive PAH emissions | Concawe. Environmental science for european refining
Polycyclic Aromatic Hydrocarbons (PAHs) | US Environmental Protection Agency
Polycyclic Aromatic Hydrocarbons | European Commission
Turbidity and Water | USGS.gov
Marintek report MT2016 F-152 ("Clipper Harald operation with scrubber")
WESP - Wet electrostatic filter
The Wet Electrostatic Precipitator (WESP) solution leads the exhaust from the main engine outlet through a honeycomb structure rigged with high voltage electrodes. The ensuing electrical field is able to filter up to 80 to 95 percent of particulate matter (PM), which is attached to the tube electrodes and flushed by water for cleaning onboard. According to WESP manufacturer Wärtsilä, the technology is incremental to Solvang's onboard carbon capture and storage (OCCS) technology.
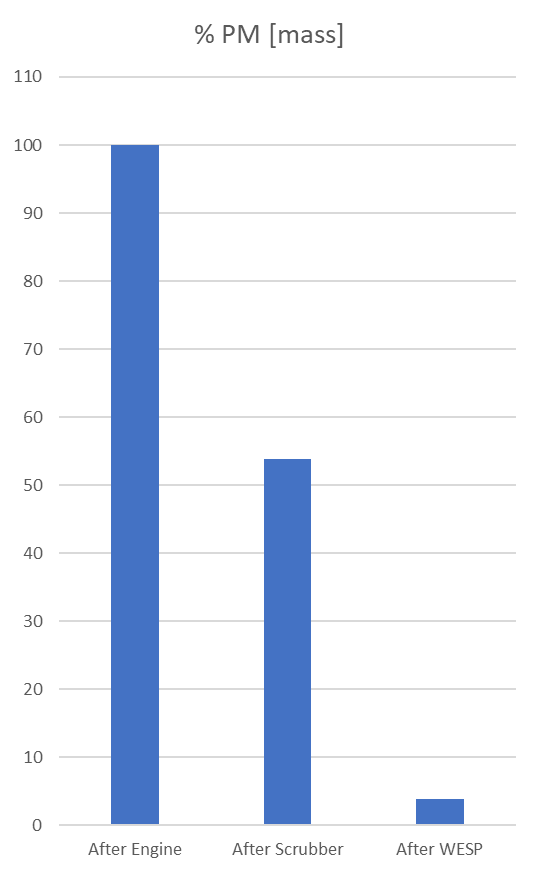
The WESP in action (activate audio)
GHG reduction for different shipping fuels
The figure below illustrates the cost of reducing the emission of one ton GHG gas.
The calculation strongly support our work for making HFO clean. It is a very cost effective solution to reduce the GHG emissions. Actually it is the only available technology with a negative abatement cost. I.e. reduce cost and GHG emissions at the same time.
Well-to-wake emissions from different fuels
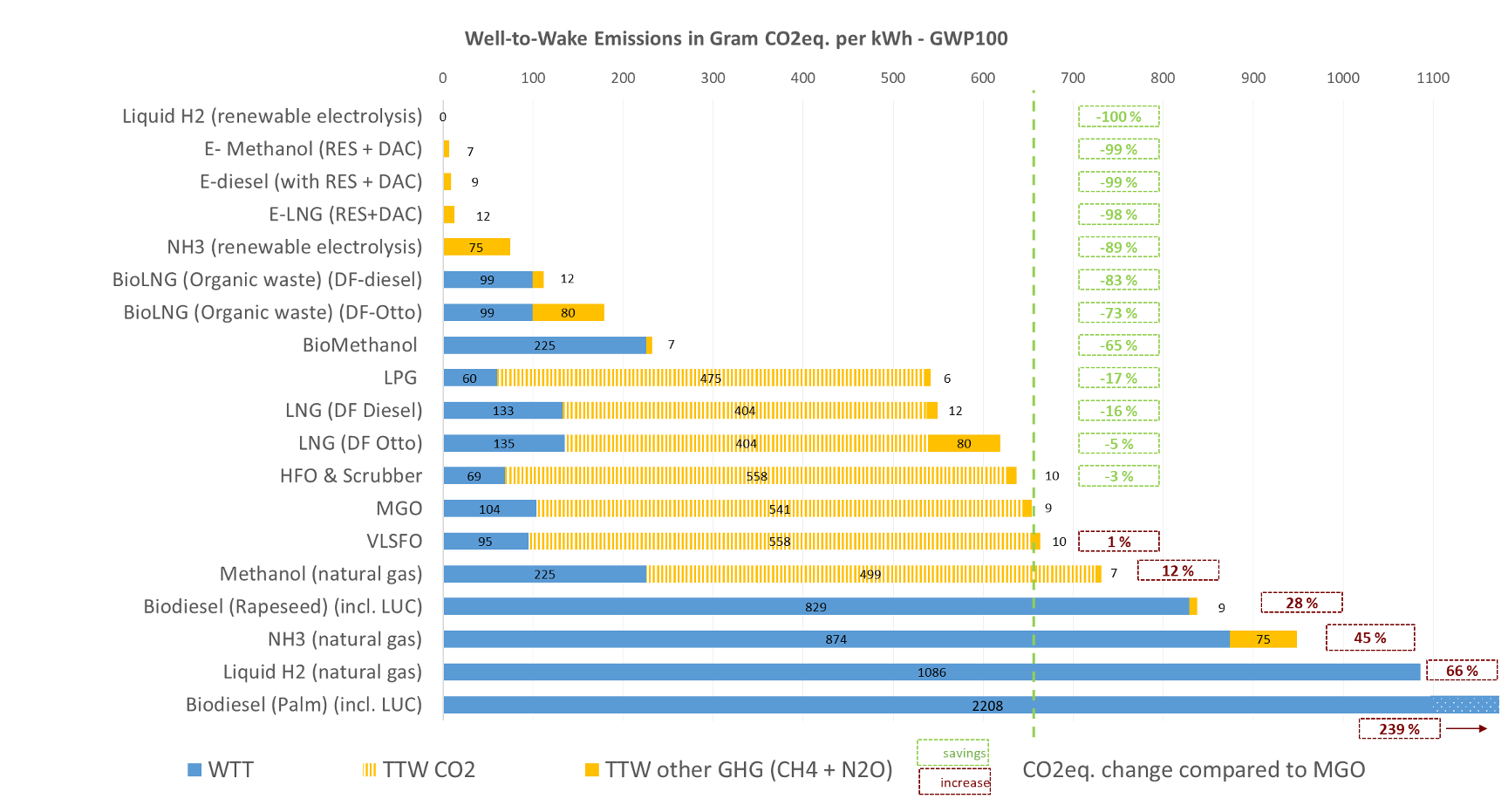
Total energy input WTW/delivered propulsion energy
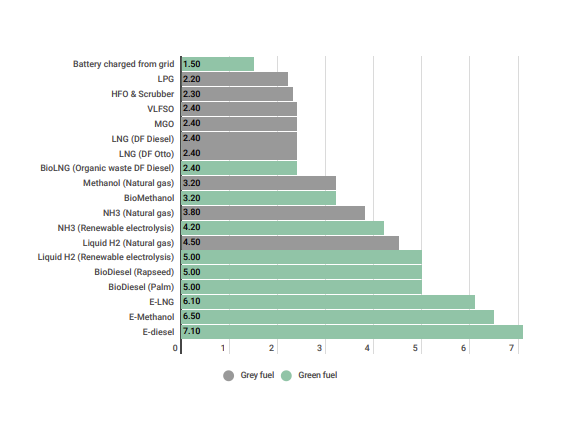
Abatement costs per tonne GHG
The calculation strongly support our work for making HFO clean. It is a very cost effective solution to reduce the GHG emissions. Actually it is the only available technology with a negative abatement cost. I.e. reduce cost and GHG emissions at the same time.
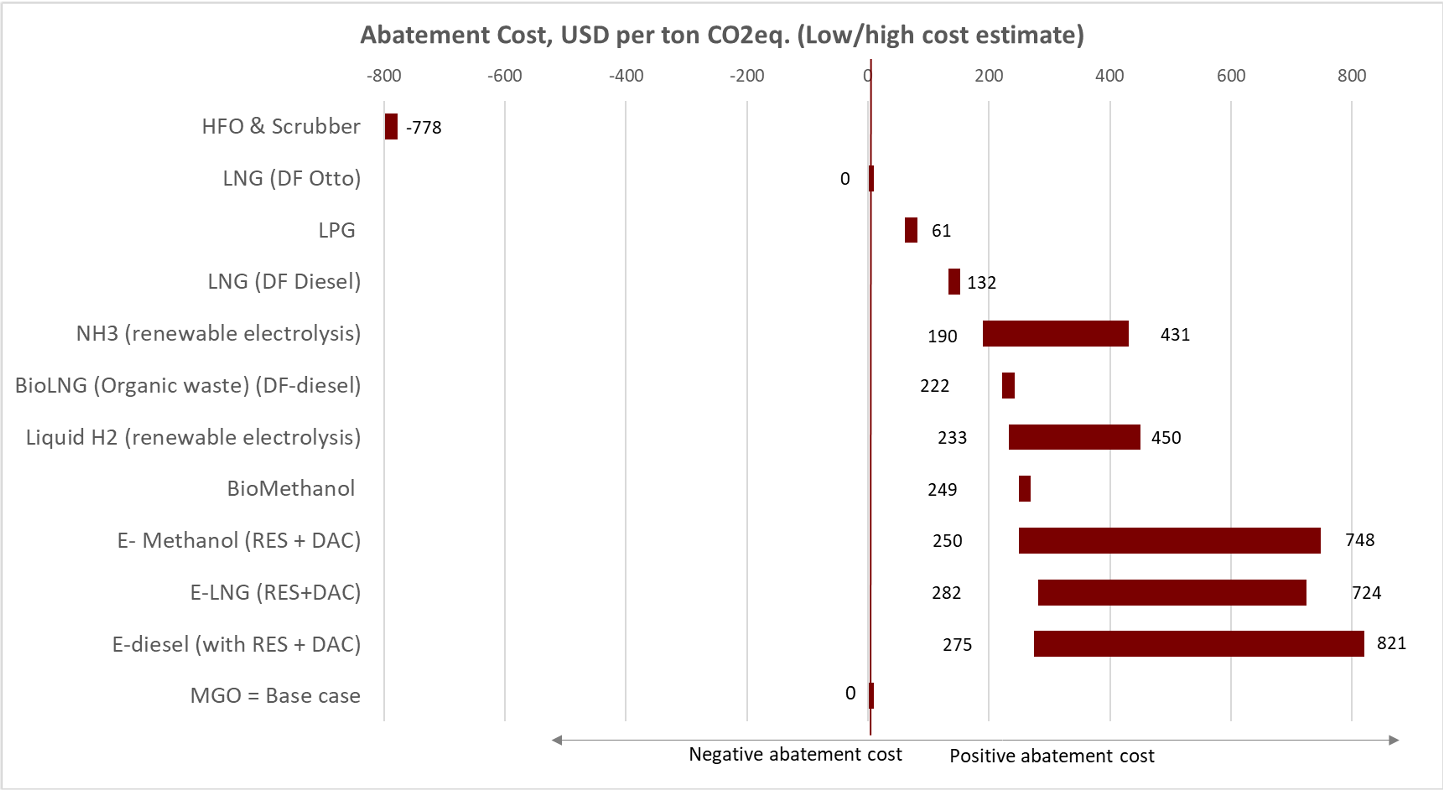
Life below water - our footprint
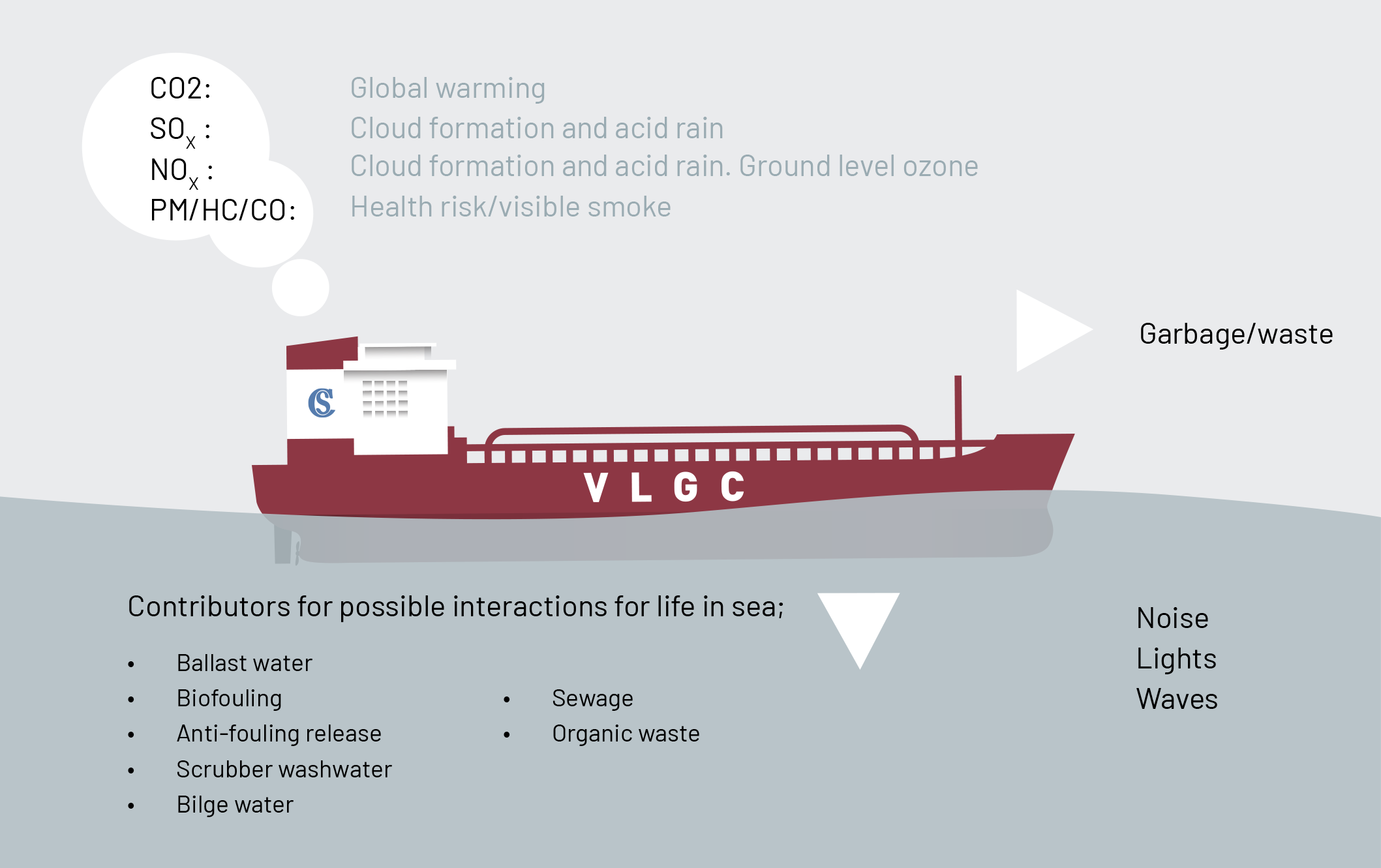
Ballast water
Solvang installed ballast water treatment systems on board all vessels. Ballast water is regarded as a high-risk emission source, as the ballast water contains marine sediments and organisms. When ships sail across the world with ballast water, species are transferred into waters where they do not belong, and they become a threat to the original marine life. This may damage the local ecosystem and could give severe consequences. All ballast water has been treated on all vessels since 2020.
Bio-fouling
Solvang uses high quality anti-foulings, and we monitor hull resistance to marine growth. The introduction of invasive aquatic species to new environments by ships has been identified as a major threat to the world’s oceans and to the conservation of biodiversity. A multitude of marine species, carried either in ships’ ballast water or on ships’ hulls, may survive to establish a reproductive population in the host environment, becoming invasive, out-competing native species and multiplying into pest proportions. Solvang uses high quality anti-foulings monitor hull resistance. In case of marine growth, this is removed by hull cleaning at the first opportunity.
Garbage/waste handling
Garbage management plan stated for all vessels. Segregation of waste to shore, waste to sea, waste incinerated on board.
Anti-fouling
All vessels have TBT-free coatings. Toxic discharges from the vessels’ anti-fouling systems harming the environment, have led to a worldwide prohibition of coatings containing TBT. All old vessels are now coated with TBT-free anti-fouling systems, along with newbuildings. Solvang works closely with suppliers, in order to find and use anti-fouling solutions which will ensure the hull’s environmental efficiency throughout the docking period.
Bilge water
All bilge water runs through separator and each run is registered in the oil record book. These discharges are covered by MARPOL 73/78 Annex 1. All waste oil and sludge is burned in the incinerator or delivered to an approved processing plant onshore.
Sewage
All vessels have urinals and holding tanks. Sewage is defined as discharges from toilets, urinals and holding tanks. MARPOL 73/78 covers these discharges, and our vessels have holding tanks that are in accordance with international regulations. Sewage dumping is only allowed when the distance from the shoreline is at least 12 nautical miles. For disinfected or finely dispersed sewage, the minimum distance is 4 nautical miles. In both circumstances the vessel shall be moving. The Company will abide by all directives in this area, but with a crew of about 25 persons, we do not consider our discharges to be a major burden to the environment.
Oil
All vessels have air seals on the propeller shaft, which eliminates the possibility for oil leaking into the sea. The risk of oil discharges is minimal, and may occur only from from thrusters. The key to minimize these discharges is good maintenance. The oil consumption on these systems is monitored precisely. Bio-oil is used in every case on thruster system where such application is approved by maker.